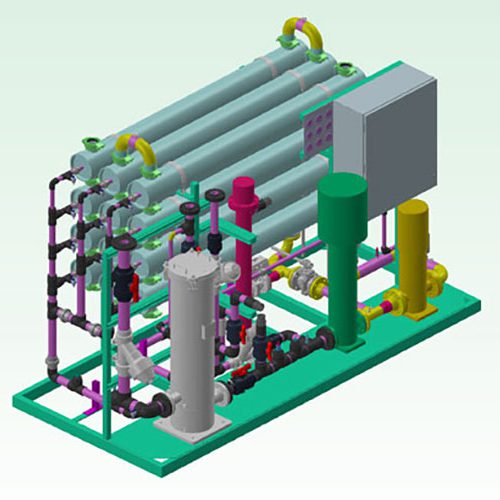
Toujours à la hauteur de vos défis
Notre client, une grande entreprise agroalimentaire, nous a demandé de concevoir un système d'osmose inverse sur mesure. L'objectif de la purification de l'eau était de pouvoir utiliser l'eau recyclée pour alimenter des chaudières ou refroidir des composants, au lieu de dépendre du système de traitement de l'eau municipal.
Le projet a présenté son lot de défis, parmi lesquels la nécessité d'ajuster le débit du système d'osmose en fonction du taux de production. Durpro a également rencontré un défi en termes d'espace ; la configuration personnalisée du système devait inclure un système plus court ainsi qu'une osmose duplex. Mais surtout, la solution devait répondre aux normes strictes de l'industrie alimentaire pour éviter toute contamination bactérienne.
Le système conçu par Durpro est un succès sur plusieurs niveaux. Grâce à sa grande flexibilité, le taux de production peut être ajusté selon les besoins. La circulation continue et le taux de recirculation élevé empêchent les bactéries de se fixer sur les parois. Le rapport de réduction optimise la performance, un défi à relever puisque l'eau chaude est utilisée dans plusieurs applications.
Économies de temps et d'argent
De plus, la recirculation de l'eau et le fait que l'eau soit réutilisée et non seulement traitée minimisent les gaspillages. En plus de bénéficier à l'environnement, le système permet également à notre client d'économiser plusieurs milliers de dollars par an en électricité, ainsi que des dizaines de milliers de dollars chaque année sur l'approvisionnement en eau municipale.
Sans oublier les économies de temps et d'argent en ce qui concerne la maintenance. Le système a été conçu pour recevoir de l'eau à différentes températures et ne nécessite pas de nettoyage constant. D'autres solutions nécessitent généralement une maintenance quatre fois par an, tandis que le système de Durpro n'a besoin d'être nettoyé qu'une fois par an.
La surveillance continue des performances fournie par le système de Durpro est un autre avantage significatif. La solution prévient notre client à l'avance lorsque la maintenance est requise, pour une planification et une production optimisées. C'est particulièrement crucial pour notre client, car la maintenance nécessite un arrêt de 24 heures. Pouvoir planifier la maintenance signifie maximiser l'efficacité de la production et minimiser les coûts associés aux arrêts de production, qui représentent pour notre client des centaines de milliers de dollars chaque heure.
Préoccupation continue pour la performance
Conformément à la réputation de Durpro, le nouveau système est doté d'instruments de surveillance avancés pour la mesure de la conductivité, de la température ou de la pression. Les données opérationnelles critiques sont normalisées, du débit de perméat à la rejection du sel ou à la chute de pression.
La relation de confiance développée au cours de ce projet est typique de l'expérience Durpro. Que vous recherchiez un système de filtration, de purification ou de traitement de l'eau, nos experts ont à cœur votre succès et livrent systématiquement des produits de qualité répondant aux normes d'efficacité les plus élevées.